WORDS
Amy Miles
It almost feels mandatory to list Lock & Co’s impressive credentials when introducing the brand. Its status as the world’s oldest hatmaker, for instance, or that it is a double Royal Warrant holder and the 34th-oldest family-run business on the planet. Then there is the tale of the postcard that arrived at its St James’s Street shop simply addressed to “The best hatters in the world, London” – now a legendary anecdote among hat aficionados. Lock’s fabled customer list, meanwhile, is worthy of its own feature.
But resting on its laurels is not in the Lock & Co handbook, and it continues to develop exciting new designs to delight longtime customers and attract new ones. This season’s offering includes limited-edition flat caps, such as the Drifter in airy herringbone linen, and a stylish striped baseball cap that will be just as at home in the Hamptons as in London Fields. These new pieces sit alongside the classics, such as Lock’s proprietary Coke bowler – created in 1849 and characterised by a domed crown and curled brim, and its Panama hats, which are still hand-woven in Ecuador.
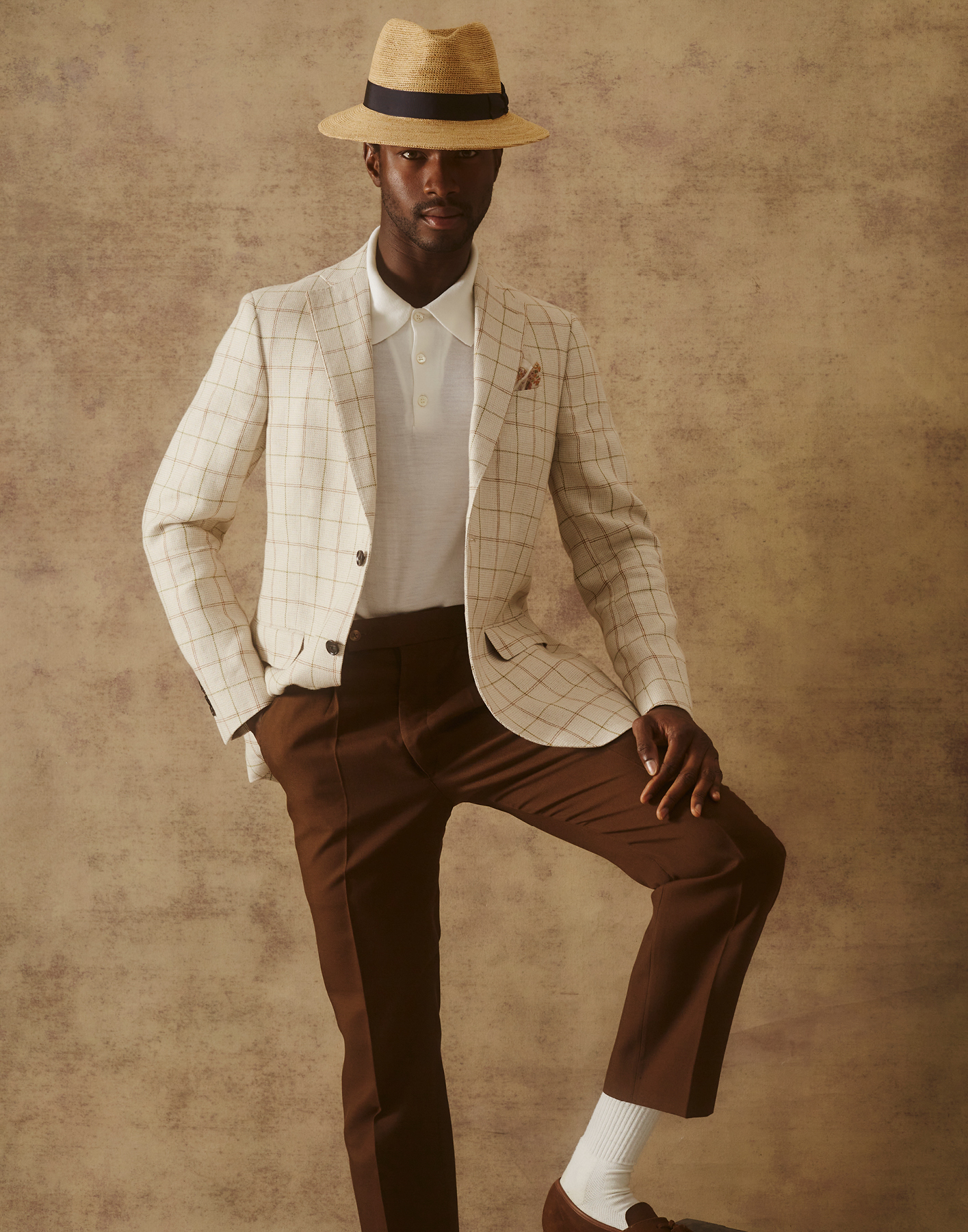
One of the keys to Lock’s longevity is the care it takes in making a well-balanced hat. Managing director Ben Dalrymple explains that new hat blocks are created by determining a specific height and profile, and a brim width that complements the crown in order to achieve the most flattering proportions. ‘We use our own blocks – some decades (if not centuries) old – for our most-loved heritage shapes and styles, and some we create for each season, ensuring that we can be as innovative as our customers wish.’
Materials selection is an important factor, too: ‘In creating a trilby or fedora, for example, we carefully consider the colour, lustre, handle, softness or stiffness (depending on the purpose), durability and ultimately, quality. The very best felts, leathers, linings and ribbons are then selected and tested,’ Dalrymple says. He adds that when it comes to fabric sourcing, excellence comes before convenience, with wool tweed brought in from Scotland, leather from Italy, satin from Belgium and silk from France. Once all the elements of that hat are finalised, Lock creates a “gold” sample, which becomes the benchmark for every future iteration.
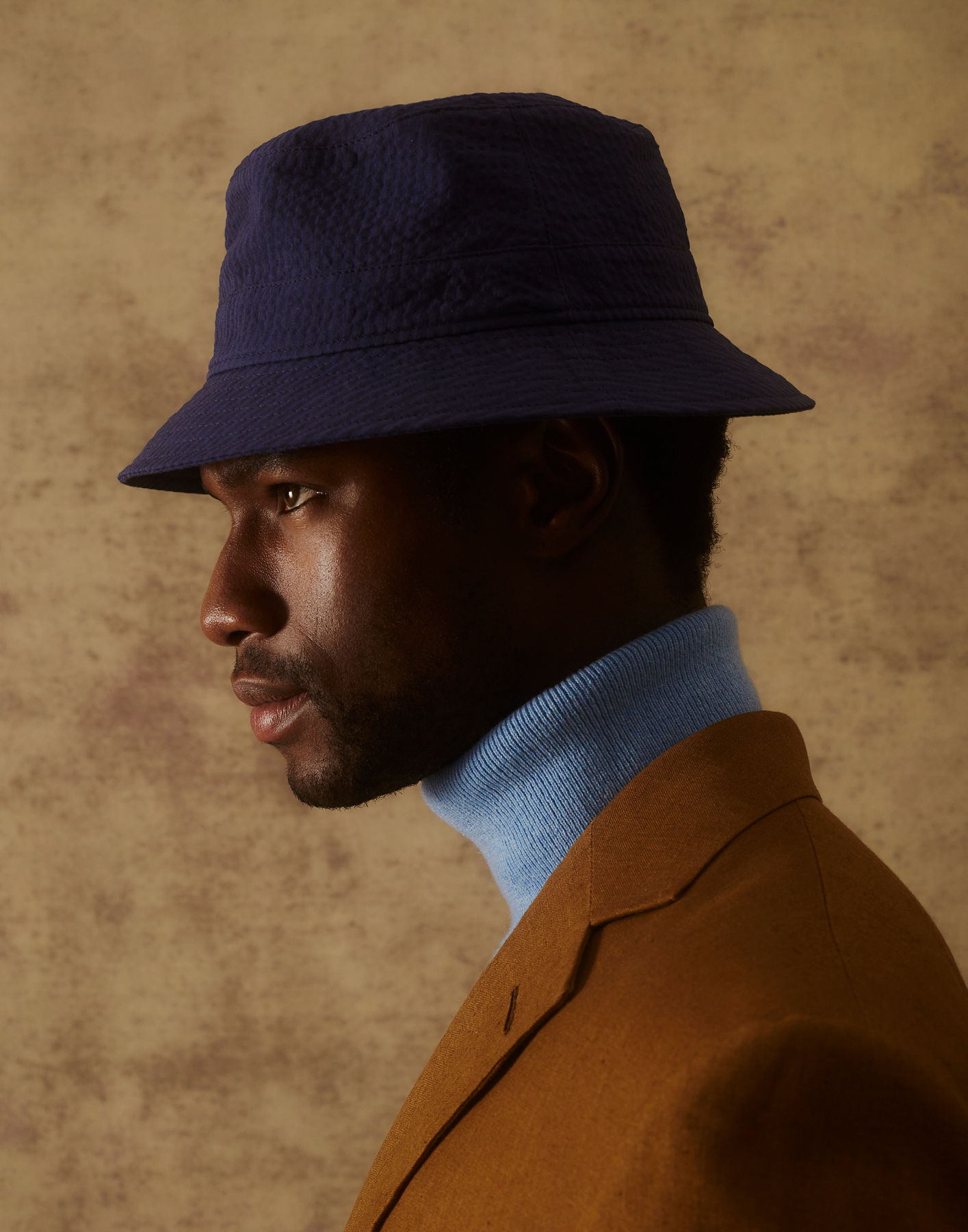
And while times have changed since the 17th century when Lock & Co was founded, many of its hatmaking techniques and tools have not. Sometimes, the old ways are indeed the best ways. Dalrymple explains that much of the craftsmanship involved in hatmaking and finishing (which is done entirely by hand) is passed down through generations of artisans and takes many years to perfect. Felt fedoras as well as trilbies, in particular, are imbued with centuries of heritage.
‘They are not woven like caps, and the felt-making industry itself is still very small, but hard-working,’ says Dalrymple. ‘Our chairman is currently the Master of The Worshipful Company of Feltmakers of London – one of the Livery Companies of the City of London. The Feltmakers were incorporated by Letters patent granted by James I in 1604, and received an extended Royal Charter in 1667.’
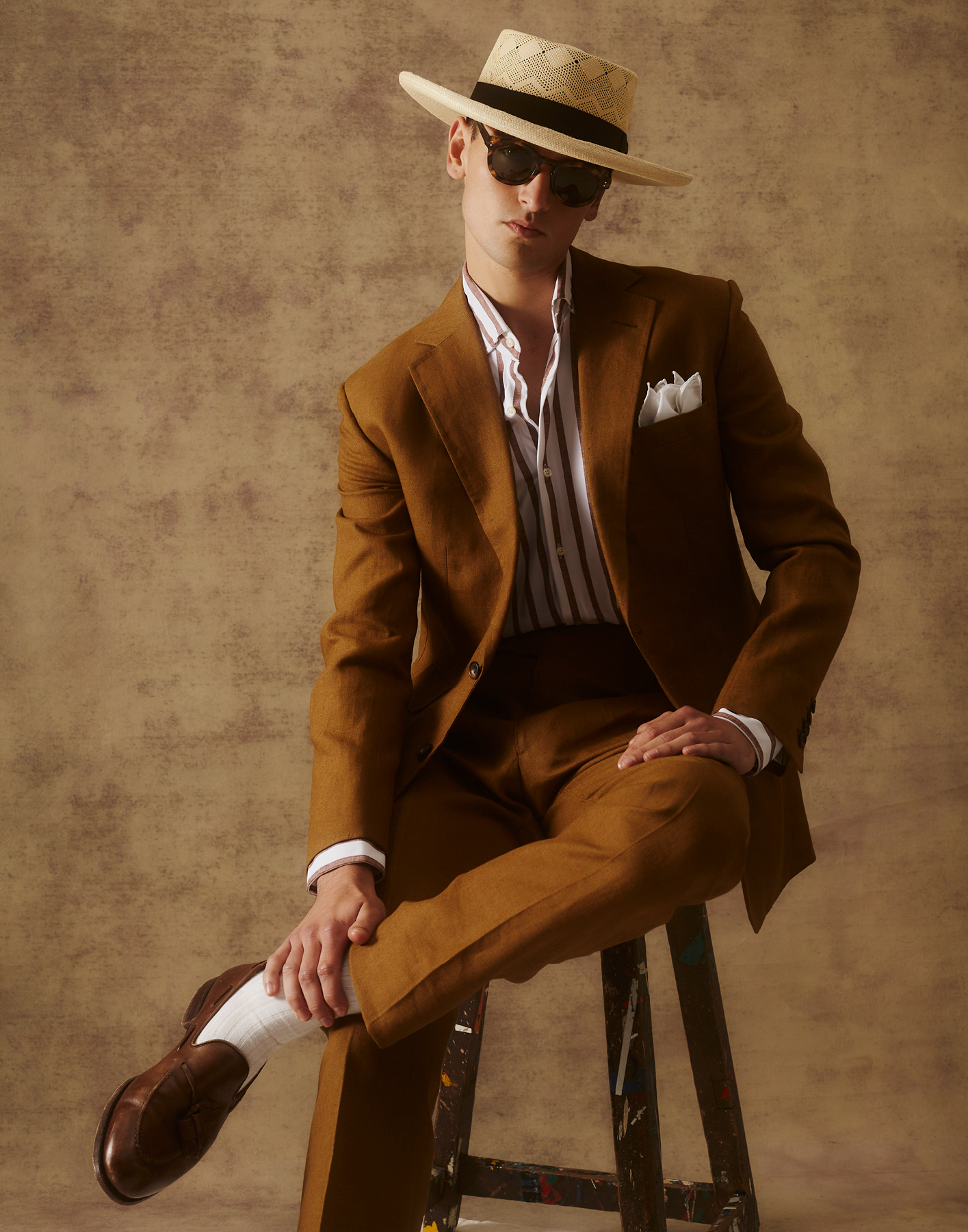
The 1600s, too, were when Lock’s famed townhouse on St James’s Street was built, and while the archive housed inside is truly incredible, the structure (originally timber) and size of the building have long proved an impossible challenge for the weight and heat of machinery required for hat blocking, meaning the company had to find other locations to make its hats from the very beginning. ‘In our atelier and workroom, we still make all of our Couture range by hand, and we can make caps and fabric hats that require fewer mechanical processes and more made-by-hand craftsmanship. All personalisation, sizing, shaping and repair work is still done on-site at St James’s Street, ensuring a perfect fit and the ability to look after your hat for life.’